When it comes to industrial screening equipment, vibrating screens play a crucial role in separating and classifying bulk materials efficiently. However, choosing the right type of vibrating screen can be challenging—especially when the options come down to linear vibrating screens and circular vibrating screens.
Both types offer unique benefits and are suited for different materials, industries, and operating conditions. Whether you’re screening aggregates, sand, chemicals, or food-grade powders, understanding the differences in design, motion, energy consumption, and application suitability is essential for making an informed investment.
Choosing between a linear and a circular vibrating screen depends heavily on the specific application, the material characteristics, and the desired screening outcome. Both types have distinct working principles, advantages, and disadvantages.
Linear vibrating screen vs circular vibrating screen
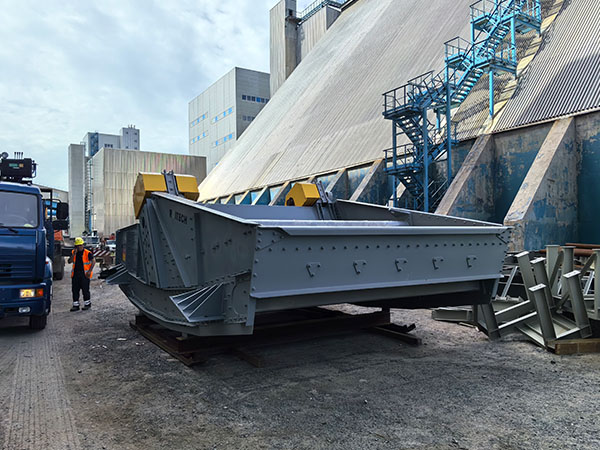
Linear Vibrating Screens
Working Principle:
Linear vibrating screens use two unbalanced motors or eccentric shafts that operate synchronously in opposite directions. This creates a linear, straight-line vibration that causes the material to be thrown upward and forward along the screen surface.
Key Characteristics:
Movement Track: Material moves in a straight line.
Vibration Exciter: Typically uses twin vibrating motors or two eccentric shafts (biaxial).
Installation Angle: Generally installed at a small inclination angle (0-15 degrees), or even horizontally for some applications.
Material Conveyance: Efficiently conveys material forward due to the linear motion.
Structure: Often rectangular or square, can be fully enclosed.
Material: Often constructed from lighter materials like stainless steel or carbon steel.
Advantages:
Precision Screening: Excellent for fine particle separation and accurate sizing.
Reduced Blinding/Pegging: The linear motion helps to dislodge material, minimizing screen hole blocking, especially with sticky or damp materials.
Efficient Dewatering: Effective in wet screening applications for moisture removal.
High Throughput for Fines: Can handle high volumes of fine, dry, or low-density materials.
Low Energy Consumption: Generally more energy-efficient for specific applications.
Environmental Control: Can be fully enclosed to prevent dust spillage, making them suitable for sensitive environments.
Versatile Screen Panels: Can accommodate various screen panels (woven wire, perforated plate, polyurethane, etc.).
Disadvantages:
Limited for Coarse/Heavy Materials: Less effective for large, heavy, or highly abrasive materials due to the lighter construction and linear motion.
Potential for Blockage with Uneven/Humid Feed: While generally good at preventing blinding, very uneven or highly humid/viscous materials can still cause issues if screen openings are small.
May Require More Maintenance: Can have higher maintenance requirements compared to circular screens in some cases, especially with more complex drive mechanisms.
Common Applications:
Food industry (sugar, grains, powders)
Pharmaceutical industry (dry powders, fine particles)
Chemical industry
Building materials (fine aggregates, sand)
Mineral processing (precision classification of fine minerals)
Dewatering and desliming operations
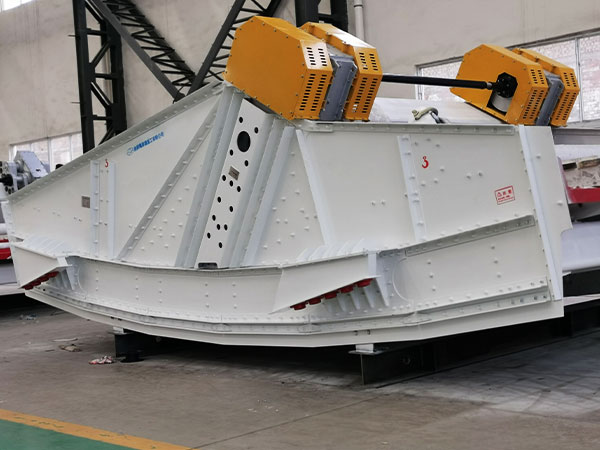
Circular Vibrating Screens
Working Principle:
Circular vibrating screens use a single eccentric weight attached to a rotating shaft (or unbalanced drive mechanism) that generates a continuous circular or elliptical motion. This motion causes the material to move in a rolling and bouncing pattern across the screen surface.
Key Characteristics:
Movement Track: Material moves in a circular or elliptical motion.
Vibration Exciter: Typically uses a single exciter (single-shaft) with an eccentric weight.
Installation Angle: Usually installed at an inclination angle (15-30 degrees) to optimize material speed and contact with the screen.
Material Conveyance: The circular motion disperses material and aids in throughput.
Structure: Often rounded in shape with multiple decks.
Material: Manufactured from thicker, more durable materials like manganese steel to withstand impact.
Advantages:
High Capacity for Coarse Materials: Excellent for screening large, coarse, and heavy materials.
Robust and Durable: Built to withstand high-speed vibrations and impact from heavy loads.
Less Prone to Material Bouncing: The circular trajectory helps keep material in contact with the screen for longer.
Simple Design, Lower Maintenance: Generally simpler in design, leading to easier maintenance for the drive mechanism.
Effective for Scalping: Ideal for initial separation of oversized material (scalping).
Disadvantages:
Less Precision for Fines: May not be as precise as linear screens for very fine particle separation.
Potential for Blinding with Certain Materials: While the motion helps, some sticky or flaky materials can still cause blinding if the material isn’t well dispersed.
Less Suitable for Horizontal Installation: Requires an incline for material flow.
Dust Control: Can be harder to fully enclose compared to linear screens, potentially leading to more dust spillage.
Common Applications:
Mining (coal, ore, aggregates)
Quarrying (stone crushing, rock separation)
Building materials (gravel, large aggregates)
Metallurgical industry
Recycling industries (screening large bulk materials)
Which One to Choose?

To make the right choice, consider the following factors:
Material Characteristics:
Particle Size:
Coarse/Large (e.g., rocks, coal): Circular vibrating screens are usually preferred due to their robust nature and high capacity.
Fine/Small (e.g., powders, grains): Linear vibrating screens excel in precision and efficiency for finer particles.
Moisture Content/Viscosity:
Wet/Sticky: Linear screens can be better for dewatering and minimizing blinding, but very high viscosity might still be challenging. Circular screens with their bouncing motion can also help prevent clogging for some moist materials.
Abrasiveness:
Highly Abrasive: Circular screens, often made with more durable materials, are better suited.
Density:
High Density: Circular screens.
Low Density/Light: Linear screens.
Desired Screening Outcome:
High Throughput & Scalping: Circular screens.
High Precision & Classification: Linear screens.
Dewatering: Linear screens.
Capacity Requirements:
Large Volumes of Coarse Material: Circular screens.
Large Volumes of Fine Material: Linear screens can also achieve high throughput for fines.
Installation Space and Layout:
Limited Height: Linear screens can often be installed more horizontally, requiring less vertical space.
Inclined Installation Acceptable: Circular screens typically require an incline.
Environmental Considerations:
Dust Control Critical: Linear screens can be fully enclosed for better dust containment.
Maintenance and Durability:
Consider the wear and tear on screen media and the frequency of maintenance based on your material and operational intensity.
In summary, if you’re dealing with heavy, coarse, or high-volume materials where robust separation is key, a circular vibrating screen is often the better choice. If your focus is on precise classification of fine or dry materials, dewatering, or applications requiring excellent dust control, a linear vibrating screen will likely be more suitable.