Vibrating screens are critical equipment in mining, aggregate, and industrial processing, but they are prone to wear due to constant vibration, material impact, and abrasion. Implementing effective wear protection solutions can significantly extend screen life, reduce downtime, and improve efficiency.
Vibrating Screen Wear Protection Solutions
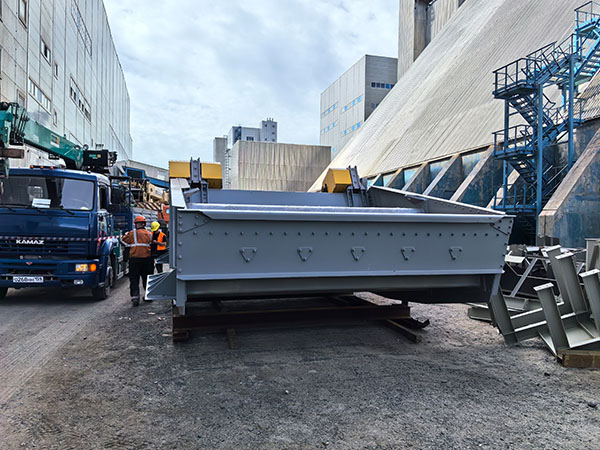
1. Screen Media Wear Protection: (The most critical wear surface)
Material Selection:
High-Carbon Steel Wire Mesh: Standard, cost-effective, good abrasion resistance for many applications. Different weaves (e.g., square, slotted) affect wear life and open area.
Stainless Steel Wire Mesh: Offers corrosion resistance in addition to abrasion resistance, suitable for wet or corrosive environments. More expensive than high-carbon.
Polyurethane (PU) Panels: Excellent abrasion resistance, especially in wet applications. Good impact resistance, noise reduction, and often longer life than wire mesh in abrasive conditions.
Modular panels allow replacing only worn sections. Can be prone to cutting by sharp materials.
Rubber Panels: Superior impact resistance, good for large, heavy feed material. Excellent noise damping. Good abrasion resistance, particularly in wet sliding abrasion scenarios. Can be less efficient (lower open area) than wire mesh. Modular options available.
Perforated Steel Plate: Very robust, used for heavy-duty scalping applications with large, impactful material. Lower open area compared to mesh. Can be made from abrasion-resistant (AR) steel.
Hybrid Screens: Combine different materials (e.g., PU frame with wire mesh inserts) to optimize open area and wear life in specific zones.
Profile Wire / Wedge Wire: Smooth surface reduces plugging and wear in some applications, often used for dewatering or specific fine screening.
Configuration:
Modular Systems (PU/Rubber): Allow targeted replacement of high-wear areas, reducing overall replacement cost and downtime compared to full-deck tensioned media.
Proper Tensioning (Wire Mesh): Crucial for wire mesh. Loose screens flap, causing premature fatigue failure and accelerated wear. Over-tensioning can also cause failure. Use manufacturer recommendations and check tension regularly.
Crowned Deck: Helps tension wire mesh properly and can aid material distribution.
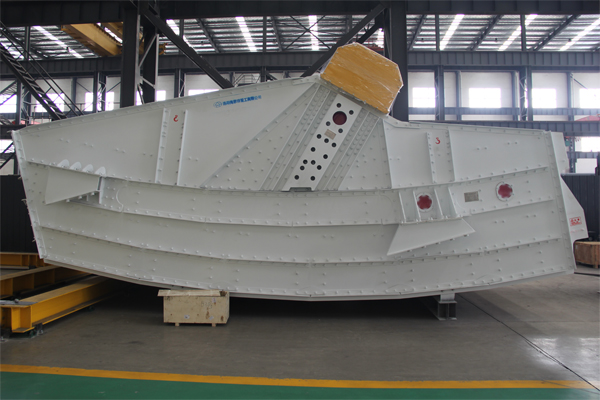
2. Feed Box / Feed Chute Wear Protection: (High impact and initial abrasion)
Abrasion-Resistant (AR) Steel Liners: Hardened steel plates (e.g., AR400, AR500) bolted or welded in place. Good balance of impact and abrasion resistance, cost-effective.
Rubber Liners: Excellent for absorbing high impact from falling material. Reduces noise significantly. Best suited where impact is the primary concern over sliding abrasion.
Polyurethane (PU) Liners: Good combination of impact and sliding abrasion resistance, especially in wet conditions.
Ceramic Liners: Extremely high resistance to sliding abrasion, but can be brittle and susceptible to cracking under direct high impact. Often used in combination with rubber (rubber-backed ceramics) to improve impact resistance. Best for fine, highly abrasive material with lower impact.
Chromium Carbide Overlay (CCO) Plate: Very high abrasion resistance due to hard chromium carbide particles in a softer matrix. Good for severe sliding abrasion, moderate impact. Can be welded or bolted.
Dead Box / Rock Box Design: Designing the feed box so that a layer of the material being processed builds up and forms a natural wear liner, protecting the steel structure underneath. Material impacts material, drastically reducing wear on the liner itself.
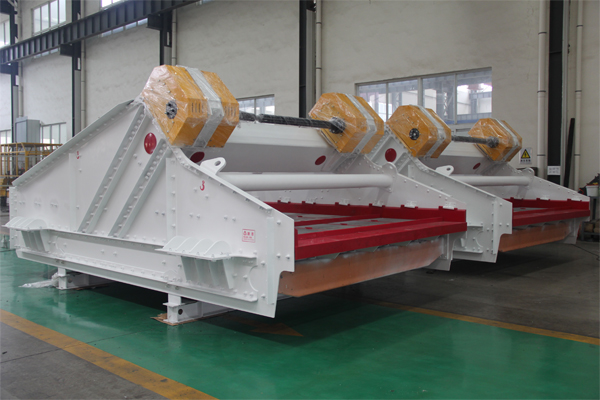
3. Side Plate Wear Protection: (Sliding abrasion from material moving along the sides)
AR Steel Liners: Most common solution, bolted for easy replacement.
Rubber or PU Liners: Reduce noise and offer good wear life, especially if there’s some impact against the sides.
CCO Plate or Ceramic Liners: Used in highly abrasive applications.
4. Discharge Lips Wear Protection: (Sliding abrasion as material exits)
AR Steel Liners: Commonly used, often thicker or harder grade than side liners due to concentrated wear.
Replaceable Bolt-on Lips: Designing the lip as a separate, easily replaceable wear component made of AR steel, CCO, or PU.
Hardfacing: Applying a wear-resistant weld overlay directly to the discharge lip area (can be done during manufacturing or as a repair).
5. Screen Deck Structure / Cross Member Protection:
Rubber or PU Capping: Covering the tops of deck support bars (where screen media rests) protects them from abrasion from the underside of the screen media or migrating fines. This is essential for modular systems and highly recommended for tensioned media.
Profiled Cross Members: Some designs use specifically shaped cross members to minimize flat surfaces where material can build up and cause wear.
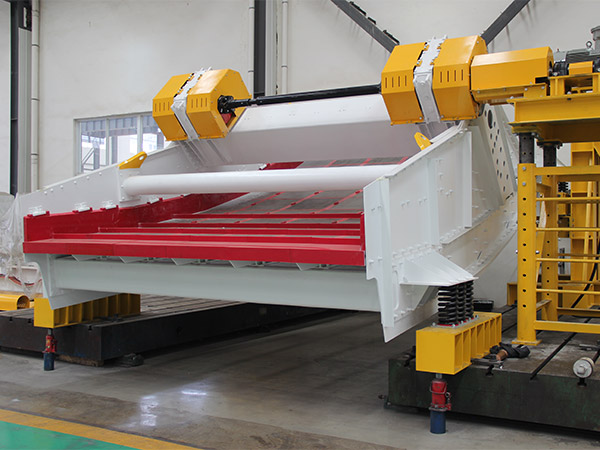
6. Operational and Maintenance Practices:
Proper Feed Distribution: Ensure material spreads evenly across the screen width. Concentrated flow drastically accelerates wear in specific areas. Adjust chute design or use distributors if needed.
Avoid Overloading: Running the screen beyond its capacity increases bed depth, reduces efficiency, and accelerates wear.
Control Feed Rate: Surges in feed can cause impact damage and overload.
Regular Inspections: Frequently check all wear areas (media, liners, structure) for wear patterns and damage.
Timely Replacement: Replace worn components before they fail catastrophically or cause damage to underlying structures.
Correct Component Installation: Ensure liners are bolted securely and screen media is installed/tensioned correctly. Loose components wear faster and can damage the screen structure.
Cleaning: Prevent material buildup, especially sticky or corrosive material, which can trap abrasive particles or cause corrosion.
Selecting the Right Solution:
The best solution depends on:
Material Characteristics: Size, shape, hardness, moisture content, corrosivity.
Application: Scalping, fine screening, wet/dry processing.
Impact Levels: Height of drop onto the screen.
Operating Conditions: Tonnage, temperature.
Budget: Initial cost vs. lifespan and replacement cost.
Maintenance Capabilities: Ease of inspection and replacement.
The best wear protection depends on the material being processed (e.g., abrasive ores vs. lightweight aggregates). Combining durable screen media, protective liners, reinforced components, and proper maintenance maximizes screen lifespan and operational efficiency.