Slow discharge from a linear vibrating screen is a common issue that can significantly reduce screening efficiency and overall plant productivity. It means material is not moving across and off the screen deck as quickly as it should.
Reasons and solutions for slow discharge of linear vibrating screen
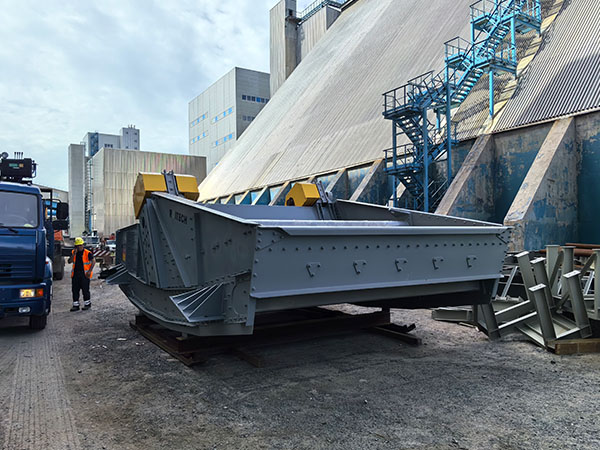
I. Reasons Related to the Screen Mesh & Deck:
Blinding or Pegging of the Screen Mesh:
Reason: Fine particles get stuck in the openings of the screen mesh (blinding), or near-size particles get wedged in the openings (pegging). This reduces the effective open area, slowing down the passage of undersize material and causing oversize material to build up and discharge slowly.
Solution:
Regular Cleaning: Manually clean the mesh with brushes, pressure washers, or air lances.
Anti-Blinding Devices: Install bouncing balls, slider rings, or polyurethane stars beneath the screen mesh. These continuously tap the mesh from below, dislodging stuck particles.
Ultrasonic De-blinding Systems: For very fine or difficult materials, ultrasonic systems vibrate the mesh at high frequencies, preventing blinding.
Self-Cleaning Mesh: Use specialized screen media with flexible wires that vibrate independently to dislodge particles.
Adjust Mesh Tension: Ensure the mesh is properly tensioned. Sagging mesh can exacerbate blinding.
Incorrect Screen Mesh Aperture (Opening Size):
Reason: If the mesh openings are too small for the desired separation or for the bulk of the material, it will naturally process material slowly.
Solution:
Re-evaluate Application: Ensure the chosen mesh size is appropriate for the material characteristics and the desired cut point.
Consider a Coarser Mesh: If possible and acceptable for the product, use a slightly larger mesh opening.
Worn or Damaged Screen Mesh:
Reason: Torn, stretched, or excessively worn mesh can lose its tension, sag, and have inconsistent openings. This can lead to material pooling in areas and inefficient conveying.
Solution:
Inspect and Replace: Regularly inspect the mesh for wear and tear. Replace damaged sections or the entire mesh panel as needed.
Insufficient Screening Area:
Reason: The screen might be too small for the volume of material being fed onto it, leading to overloading.
Solution:
Reduce Feed Rate: If possible, reduce the amount of material being fed to the screen.
Upgrade Screen Size: If the feed rate cannot be reduced, a larger screen or an additional screen may be necessary.
Sagging Screen Mesh:
Reason: Improper tensioning or wear can cause the mesh to sag. Material accumulates in the sagged areas, slowing its progress.
Solution:
Proper Tensioning: Ensure all tensioning bolts and mechanisms are correctly adjusted according to the manufacturer’s specifications.
Support Bars: Check if support bars beneath the mesh are adequate and in good condition.
II. Reasons Related to Vibration Parameters:
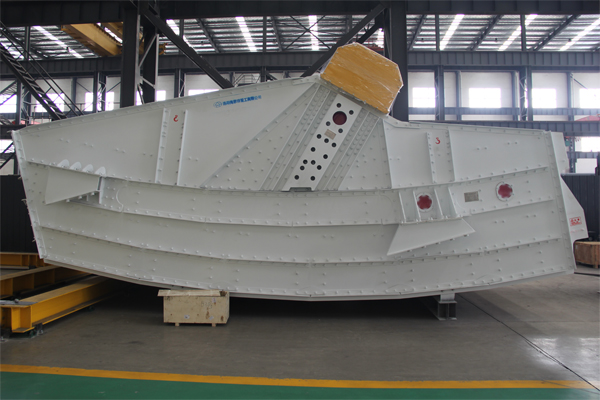
Incorrect Stroke (Amplitude):
Reason: If the stroke (the distance the screen moves with each vibration) is too small, the material won’t be lifted and thrown forward effectively, especially coarser or heavier materials.
Solution:
Adjust Eccentric Weights: Most linear screens allow stroke adjustment by adding or removing counterweights on the vibrator motors or exciter. Consult the manual.
Check Motor Health: A failing motor might not achieve full power, reducing stroke.
Incorrect Frequency (Speed/RPM):
Reason: If the vibration frequency is too low, the material won’t receive enough “pushes” per minute to travel efficiently.
Solution:
Check Motor Speed: Ensure motors are running at their specified RPM. This can be affected by VFD settings or power supply issues.
VFD Adjustment: If a Variable Frequency Drive is used, ensure it’s set correctly.
Incorrect Throw Angle (Angle of Vibration):
Reason: Linear screens vibrate at a specific angle relative to the screen deck (typically 30-60 degrees, often 45 degrees). If this angle is too flat, the material won’t be conveyed forward effectively.
If it’s too steep, it might bounce too high and not travel forward quickly.
Solution:
Adjust Exciter/Motor Position: Some screens allow adjustment of the exciter’s angle relative to the screen body. Consult the manual.
Check Motor Rotation (for dual motor exciters): Ensure both motors are rotating in opposite directions and are synchronized correctly. If one motor fails or runs backward, the linear motion will be compromised.
Insufficient or Unbalanced Vibration:
Reason: Worn bearings in motors/exciters, loose mounting bolts, broken springs, or a failing motor can lead to reduced or uneven vibration.
Solution:
Inspect and Replace Bearings: Listen for unusual noises and check for overheating.
Tighten Mountings: Ensure all motor and exciter bolts are secure.
Inspect and Replace Springs: Broken or fatigued support springs will dampen vibration.
Check Motor Synchronization: For dual-motor screens, ensure they are synchronized.
III. Reasons Related to Material Characteristics:

High Moisture Content:
Reason: Wet or sticky material tends to agglomerate, blind the screen, and resist flowing freely.
Solution:
Pre-Drying: If feasible, dry the material before screening.
Screen Media Choice: Use polyurethane or rubber screens, which can have better anti-stick properties than wire mesh for some materials.
Anti-Blinding Devices: As mentioned above, these are crucial for sticky materials.
Heated Screen Decks: In some applications, heated decks can reduce sticking.
Sticky or Cohesive Material:
Reason: Similar to high moisture, naturally sticky materials (e.g., clays, some powders) will adhere to the screen surface.
Solution:
Specialized Screen Media: Polyurethane, rubber, or non-stick coatings.
Aggressive Anti-Blinding: Ultrasonic systems might be necessary.
Flow Aids: Consider adding small amounts of flow-promoting agents if product quality allows.
IV. Reasons Related to Operational & Installation Factors:
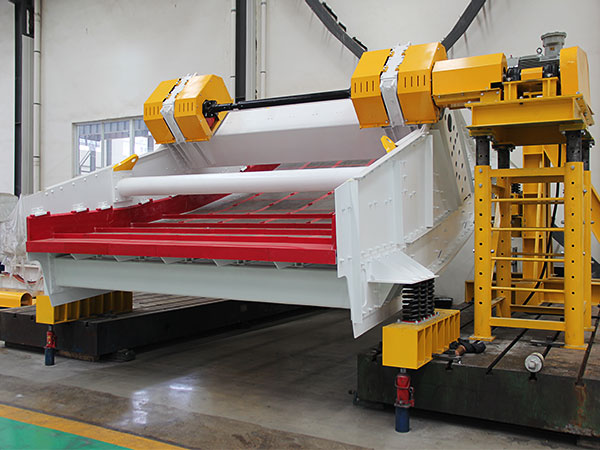
Overfeeding:
Reason: Feeding too much material onto the screen overwhelms its capacity. The bed depth becomes too thick for efficient stratification and conveying.
Solution:
Reduce Feed Rate: Adjust the upstream equipment or use a feeder to control the material flow.
Ensure Even Feed Distribution: Spread the material evenly across the width of the screen.
Incorrect Screen Inclination Angle:
Reason: Linear screens are typically installed at a slight decline (e.g., 0-10 degrees, often around 5 degrees) to aid material flow. If it’s too flat or even slightly uphill (for dewatering applications, uphill inclination is used, but general screening is downhill), material will move slowly.
Solution:
Adjust Inclination: Check and adjust the screen’s installation angle as per manufacturer recommendations for your specific application.
Obstruction at the Discharge Point:
Reason: Material backing up from the discharge chute or downstream equipment can prevent material from exiting the screen freely.
Solution:
Clear Obstructions: Ensure discharge chutes are clear, properly angled, and adequately sized.
Check Downstream Equipment: Ensure downstream conveyors or processes can handle the screen’s output.
Uneven Feed Distribution:
Reason: If material is fed only to one side or a small section of the screen, that area becomes overloaded while other parts are underutilized, leading to inefficient screening and slow overall discharge.
Solution:
Install/Adjust Feed Chute or Spreader: Ensure the feed arrangement distributes material evenly across the entire width of the screen deck.
Troubleshooting Steps – A General Approach:
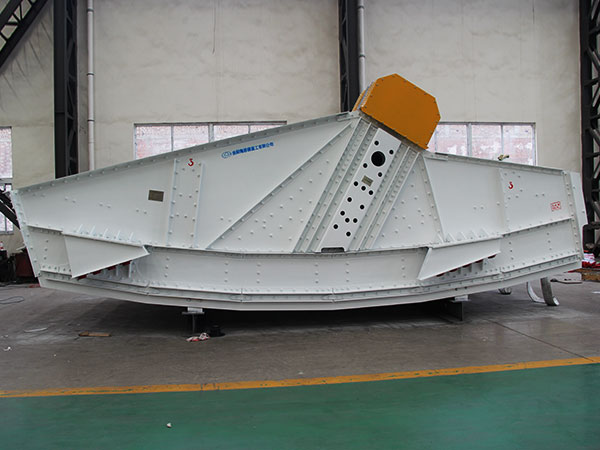
Safety First: Always lock out and tag out the equipment before any inspection or maintenance.
Observe: Watch the screen in operation (from a safe distance). Note where material is building up, how it’s moving, and any unusual noises.
Consult the Manual: Refer to the manufacturer’s troubleshooting guide and specifications.
Check the Easiest Things First:
Is the screen mesh clean?
Is there any obvious damage?
Is the discharge chute clear?
Systematic Inspection:
Mesh: Condition, tension, aperture.
Vibration: Feel the vibration (carefully), listen for odd sounds, check motor temperature, observe stroke pattern (if possible with strobe light or by watching material).
Drive System: Belts (if any), motor couplings, motor rotation.
Structure: Springs, mounting bolts.
Feed & Discharge: Evenness of feed, obstructions.
Measure Parameters: If you have the tools, measure stroke, RPM, and screen angle.
Make One Change at a Time: When implementing solutions, change one variable at a time to isolate the effect.
By systematically going through these potential causes and solutions, you should be able to identify and rectify the reason for slow discharge from your linear vibrating screen. If the problem persists, contacting the screen manufacturer or a specialized service technician is advisable.