The normal operation of the equipment can only be ensured by operating the vibrating screen in accordance with the correct safety regulations during the use of the vibrating screen. Today, the vibrating screen manufacturer will introduce to you the safety operation regulations of the high-frequency dewatering vibrating screen that we need to abide by!
Precautions for the installation of high-frequency dewatering vibrating screen
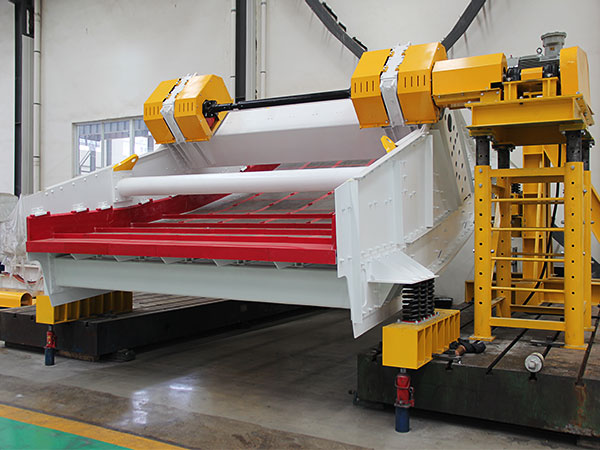
(1) When the vibration exciter is installed and repaired, it shall not be beaten hard or have a different phenomenon, and ensure that the original bearing is used and shall not be interchanged.
(2) The thickness and quantity of the eccentric block or counterweight plate attached to the eccentric block must be the same, and the radial clearance of the bearing should be C3 grade.
(3) The connection between the universal joint and the vibration exciters on both sides must be concentric, the eccentric blocks on both sides are in the free plumb position, and the universal joint connecting bolts can pass through smoothly; if there is any deviation during installation, check the universal joint Whether the joints at both ends of the section are concentric, do not swing the eccentric block angle for installation.
(4) The vibrating screen should be installed with springs with the same stiffness. The spring stiffness on both sides of the feeding end and the discharging end should be as consistent as possible, and the allowable height difference does not exceed 3mm.
(5) Both sides of the support seat of the rubber spring of the vibrating screen should be in the same horizontal plane, and the error is between 2-4mm to ensure that the materials on the screen surface advance evenly.
(6) When using electric welding to install or disassemble parts, the ground wire must be directly fixed on the welded workpiece and as close as possible to the welding point, and the welding current must not pass through any bearings or joints.
(7) In principle, welding should not be performed on the side plate. Depending on the current environment, if connecting components are required, the side plate should be drilled and then connected with bolts.
(8) The universal joint must be concentric, and a protective device must be installed to prevent it from breaking and falling and hurting people.
Precautions for the use of high frequency vibrating screen

1. Understand equipment related knowledge
The operator should ensure that the operator understands the scope of use and technical performance parameters of the equipment; has sufficient understanding and mastery of the structure, principle and common sense of maintenance of the equipment; familiar with the process flow and equipment control of the system; keep in mind the high-frequency vibrating screen Safe operating procedures.
2. Check before operation
(1) The area around the equipment should be checked to ensure that no personnel are left behind to avoid personal injury when the machine is turned on.
(2) Check whether the feeding, discharging chute and under-sieve chute are unblocked.
(3) Check whether the sieve plate and bead bolts are loose, as well as the wear of the sieve plate.
(4) Check whether the V-belt and flexible sheet are in good condition, whether the tightness is appropriate, and whether there is damage. If there is damage, it should be replaced in time.
(5) Check the connection between the universal joint and the connecting bolts of the transition pressure plate, and whether the rubber spring is damaged.
(6) Follow the sequence of the process system to ensure that the empty screen is started and all safety equipment is in a safe and operable state.
(7) The vibrating screen must be started under no load, and the material can be fed after the amplitude is stable.
3. Observation during operation
(1) Observe the distribution of materials on the screen, and make appropriate adjustments if necessary to ensure uniform distribution of materials on the screen.
(2) Observe whether the vibration frequency and amplitude of the vibrating screen are abnormal, and whether the operation is stable.
(3) Check the temperature of the motor, vibration exciter and transmission bearing seat.
(4) Observe whether there are abnormal noises such as collisions and knocks during the operation of the vibrating screen. If it is found, it must be stopped in time.
(5) Check the vibration damping of the rubber spring.
(6) Under normal operating conditions, the bearing temperature should not exceed 45 degrees.
4. Parking precautions
(1) The amplitude of over-resonance of the vibrating screen during startup and shutdown is 5 times of normal, and it should not exceed 8 times.
(2) In any case, as long as an accident occurs, the equipment should be stopped first before contacting the centralized control room and relevant positions.
(3) Under normal circumstances, the sequence of the process system should be followed, and the vibrating screen should be stopped under no load, and must not be stopped with materials.
(4) Pay attention to the large-amplitude swing when parking to ensure the safety of the equipment, and remember to abide by the safety operation rules of the high-frequency vibrating screen.
Precautions for maintenance of high frequency vibrating screen
(1) After replacing the drive belt, it is necessary to re-check whether the outer end faces of the two pulleys are on the same level.
(2) After the overhaul is completed or the electrical components are replaced, the steering must be checked to ensure the safe use and operation of the vibrating screen.
(3) After the equipment is overhauled, the vibration exciter must be turned by hand, and the main shaft should rotate flexibly without friction and jamming.
(4) Regularly check the connection parts of each bolt, which must be firm and reliable, and all bolts must not have any looseness.
(5) Regularly check the wear and tear of the sieve plate.
(6) Check the side plates and beams of the vibrating screen once a month.
(7) Regularly check the rubber spring, V-belt, flexible connecting piece and universal joint.
(8) Lubricate each lubricating point and replace the lubricating oil according to the equipment requirements.
(9) Overhaul the vibrating screen once a year, remove all the vibrating screens for cleaning and oil change, carry out a single careful inspection of the bearings, and replace them if necessary.
The above is a very detailed introduction to the safety operation rules of high-frequency vibrating screen, mainly about the operation rules of installation, use, maintenance and other aspects. We can make a relevant understanding. At the same time, if you encounter any problems in operation, you can contact us