As an important screening component of the vibrating screen, the screen is in direct contact with the material during the screening process, so the screen is the main vulnerable part in the vibrating screen system. Once the material is selected incorrectly, it is very easy to cause the screen to be worn and damaged, which affects normal production and increases the production cost. Therefore, if you want to choose the right vibrating screen, you must first understand the materials of the commonly used vibrating screens.
The material of the vibrating screen
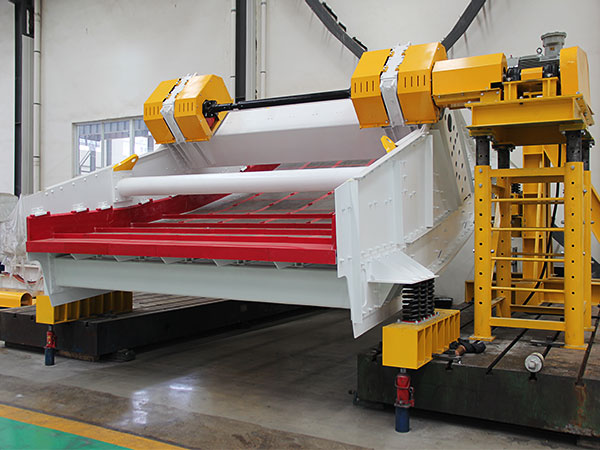
1. Stainless steel screen
Stainless steel screen materials are mainly 201, 201, 302, 304, 304L, 316, etc., which have good acid resistance, alkali resistance, and rust resistance; high strength, tensile strength, toughness and wear resistance, durability, and high temperature oxidation resistance. , 304 stainless steel screen with a nominal temperature of 800 ℃, 310S stainless steel screen with a nominal temperature of 1150 ℃; normal temperature processing, that is, easy plastic processing, making the use of stainless steel screen diversified; high finish, no surface It is convenient and simple to handle and maintain. Stainless steel screens are often used for screening and filtering under acid and alkali environmental conditions, as well as mud screens in the petroleum industry, and screens in the chemical and chemical fiber industries.
2. High manganese steel screen
Among many materials, the quality of high manganese steel screen is relatively reliable. It is a kind of screen product woven by manganese steel mesh wire with a diameter of 1.6mm-12mm. It adopts embedded weaving method. The overlapping point of warp and weft is not prominent. The screen surface is flat and the force is even. Plasticity and toughness can achieve better results, while the service life is more guaranteed. High manganese steel has high strength, rigidity and bearing capacity. When subjected to strong impact and friction, the surface will produce strong work hardening due to plastic deformation, and the surface hardness can be increased to above HRC60, thereby obtaining high wear resistance. , While the interior still maintains high plasticity and toughness. In addition, when the old surface is worn out, the new surface will form a wear-resistant layer, so the service life can reach 4-8 times that of ordinary screens. It is mostly used in large-scale mining industries. It can also be used as a protective screen for mechanical vibrating screens, Drum screen machine, electromagnetic high frequency screen machine and asphalt mixing machine, etc.
3. Punching screen
Punching screen refers to the screen that uses a punch to punch out the target pattern in the plate to be processed. Generally, it is made of stainless steel, aluminum plate, cold and hot steel plate, copper plate, PVC film and other materials. The hole type is more selective and has long Holes, square holes, round holes, hexagonal holes, scale holes, stretched shaped holes, etc. Perforated screens have the characteristics of light weight, non-slip, beautiful appearance, and good filtering performance. They are often used in environmental protection noise control barriers in traffic and municipal facilities, and mine screens, mine screens, I-shaped screens, etc.
4. Polyurethane screen
Polyurethane screens are also easier to use and have better abrasion resistance. Polyurethane itself has very high elastic modulus, high strength and impact absorption, high wear resistance, and high tensile strength, so its bearing capacity is relatively high. It is more than 2.5 times that of rubber sieve plates, and its service life is 8-10 times longer than that of ordinary metal sieve plates, 3 times that of stainless steel screens, and 3.9 times that of natural rubber. It is the current screen material with better wear resistance. . The production material of the polyurethane screen is a polymer organic elastomer, which has excellent abrasion resistance, flexibility resistance, and large load-bearing capacity. It has been specially treated to ensure that it will never delaminate under long-term alternating loads.
5. Carbon steel screen
Vibrating screens made of carbon steel are rare. Although they are low in cost and have a certain degree of corrosion resistance, they have poor wear resistance and are not more stable than stainless steel and non-metallic materials. The amount of nickel is low, the material is hard, and it is easy to break, causing the screen of the vibrating screen to be damaged too quickly, so the application is relatively small.
The choice of vibrating screen
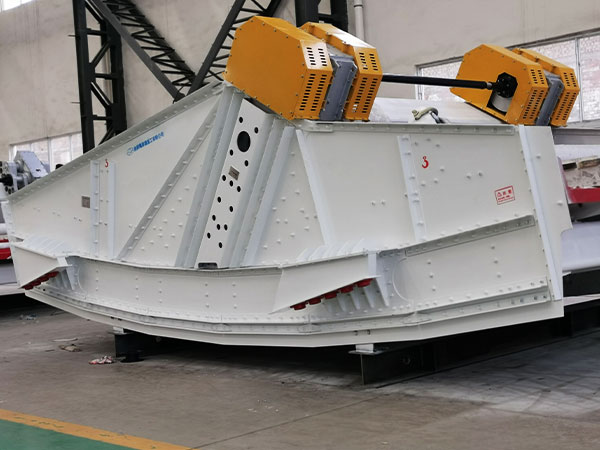
1. Choose according to materials
First of all, you must clarify what material you are sieving, and when you buy a vibrating screen. Then, according to the size of the sieved material particles, we can choose the sieve that can meet my needs for sieving. Describe the technical parameters of the screen mesh, wire diameter, aperture, diameter, material, effective screen surface, etc. The length unit is usually millimeters as the standard.
2. Choose according to the material
The material of several vibrating screens is introduced above, and the characteristics of each material are also explained in detail. Among the metal materials, the high-manganese steel screen is the better quality, but the cost is relatively high. Among non-metallic materials, polyurethane screens are the one that is easier to use.
3. Choose according to wear resistance
After clarifying the materials to be screened, look at the wear resistance of the screen. Because the materials screened by the mine vibrating screen often have higher strength, or in some chemical industries, the screened materials are corrosive, so the screen of the vibrating screen is required to have a certain degree of wear resistance, otherwise the screen Prone to breakage and high wear rate.
4. Choose according to the opening rate
The opening rate refers to the ratio of the area occupied by the screen holes to the area occupied by the screen surface. The larger the effective screening area, the greater the productivity per unit area of the screen surface and the higher the screening efficiency; the opening rate of the screen surface It is an important parameter to measure the quality of the screen surface; it should be considered not to reduce the strength of the screen surface and significantly shorten the service life of the screen surface; the screen surface of the vibrating screen is evenly distributed with holes of a certain size and shape, which are commonly called sieve holes. ; When sieving materials on the screen surface, the materials passing through the sieve holes are called under-screen products, and the materials remaining on the screen surface are called over-screen products.
The installation steps of the vibrating screen

1. Screen selection: Select the screen with the same mesh number. This is important. If the mesh number of the screen does not match, it will directly affect the accuracy and output of the screened materials;
2. Laying the screen: When installing the screen, the screen should be laid flat on the pallet, and the screen should be flattened as much as possible (but not too strong, otherwise it will affect the life and accuracy of the screen), and then use the fastening device to The screen is fixed on the net frame. Here to explain: Generally, the three-dimensional rotary vibrating screen frame is a letter grid frame. The screen mesh can be pressed on the mother mesh frame by a fastening device. The ultrasonic vibrating screen mesh is directly glued to the mesh frame, and only needs to be tightened and pasted during installation;
3. Fastening: After the screen is fastened to the mother frame, check whether the surrounding screens are all compressed on the mother frame. If slack is found, it should be adjusted reasonably;
4. Debugging: After the linear vibrating screen is installed, a little material should be used to test the cloth and screening of the screen. If the material is transported uniformly, and the classification is accurate, there is no mixing phenomenon, then it can be put into use; On the contrary, if there is unevenness such as deviation or accumulation, the flatness and uniformity of the screen surface of the screen should be adjusted; if there is a mixing phenomenon, the sealing of the linear vibrating screen and whether it is compressed should be checked.
The installation precautions of the vibrating screen
1. Note that you must choose a screen with a thicker wire diameter, because the installation of a linear screen is relatively cumbersome.
2. When cutting, the screen width should be the same as the net frame, and the length must be 50~70mm longer than the net frame.
3. When installing, the screen must be tensioned, because the tension of the screen is an important factor affecting the screening efficiency.
4. When installing the clear net pinball, you must pay attention to the difficulty of screening the material and the number of meshes, and it cannot be installed blindly.
5. If the specific gravity of the material is large or the mesh number of the screen is high, a suitable support mesh should be added under the screen. The purpose is to play a supporting role, reduce the pressure of the material on the screen, and prolong its service life. .
6. After the mesh frame is assembled to the screen box as required, remember to extend the grown screen into the corresponding outlet to avoid mixing.
7. When installing the pressure plate, be sure to pay attention to its flatness, and line it with a more flexible sponge sealing tape to evenly lock it, because this is the key to preventing mixing and an important factor that affects the service life of the screen.
The above is the introduction to the material of the vibrating screen. The material of the vibrating screen is a point that many users focus on when choosing a vibrating screen. When choosing a screen, it must be based on the characteristics of the material. The screen is wear-resistant. The combination of performance and opening rate is selected, so that the vibrating screen can also have a higher screening efficiency.